Inverted Module Test
Inverted module tests, meticulously designed and executed, play a pivotal role in ensuring the reliability and functionality of critical components. By seamlessly integrating automation, precision, and real-time monitoring, these tests verify the performance of modules—whether in automotive airbags, servo drives, or other safety-critical systems. The significance lies in reducing errors, enhancing product quality, and ultimately contributing to safer, more efficient operations.
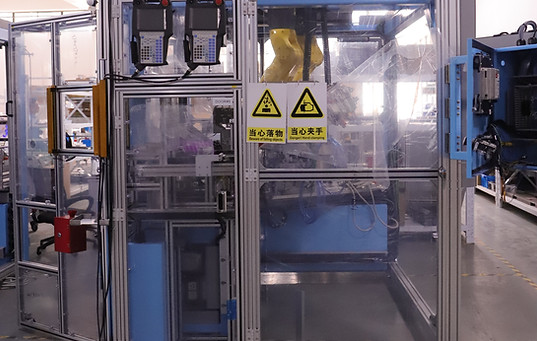
1.Introduction:
The equipment is used for S200 servo drive test. As a fully automated test equipment for Siemens' latest series S200 series products, the station has achieved many advantages such as compatibility with many products, unmanned testing and digital monitoring. Among them, it is compatible with the full range of S200 products, and the pick and place of the product is grabbed by the robot from the belt line, without manual pick-up, and the test is automatically transferred to the next station.
2. Features:
(1) Unmanned automatic operation
(2) The product has high compatibility, no need to replace any tooling, etc., all are compatible
(3) The equipment is stable and efficient
(4) Modular design, convenient and fast maintenance
(5) Intelligent and digital.
3.The significance of the project:
Provide stable solutions for customers to realize automatic testing of products.

1. Introduction:
The equipment is used to test the Siemens V90 servo drive connection. There are many models involved, there are 200V FSA/FSB/FSC/FSD and 400V FSA/FSB/FSC a total of seven categories, each category is subdivided into PN/PTI two a total of 14 subcategories, each subcategory because of the different functions tested, a total of about 50 products. The test process is fully automated and adopts a floating structure of the full interface structure to ensure the stability and reliability of the interface.
2. Features:
(1) The equipment is stable and efficient
(2) Modular design, convenient and fast maintenance
(3) The product has high compatibility, no need to replace any tooling, etc., all are compatible.
(4) Structural electrical and upper computer integration to meet customer needs in an all-round way.
3. Project significance:
Effectively improve the production capacity of customer production lines, reduce employee labor intensity, ensure product quality, and reduce test error rate.

1. Introduction:
During the assembly process of the upper shell of the Siemens V20 inverter, it is necessary to affix the customer's identification note to a more accurate label frame on the top, and the labeling accuracy of the upper and lower left and right is ±0.25mm, which makes the factory product manufacturing more digital and lean.
2. Features:
(1) high precision, labeling accuracy of ±0.25.;
(2) High accuracy, 99.9% accuracy;
(3) There is a re-inspection function after pasting;
(4) Digitalization and leanness of production capacity;
3. Project significance:
It improves the degree of automation of customers, reduces the labor intensity of employees, improves the accuracy and stability of product inspection, facilitates production management and realizes the automation and digitalization of the whole line.

1. Introduction:
This device is used to install V20 servo driver wiring locks and screws. In response to the complex shape and high installation accuracy of the lock, our company has developed this equipment for the customer. The equipment adopts a vibrating disc feeding method, with a unique cylinder feeding mechanism at the front end for precise positioning, and uses an optical fiber sensor to detect the front and back of the locking plate to prevent errors; After the lock is installed, high-precision laser detection is performed to determine if it is OK; For screw tightening, torque feedback and angle discrimination are provided to ensure product quality after installation.
2. Features:
(1) Stable equipment and high efficiency
(2) Accurate judgment and quality assurance
(3) Increase production capacity
3. Project significance:
Effectively improving customer production line capacity, reducing employee labor intensity, ensuring product quality, and reducing installation error rates.